eSimOptimizer TM
eSimOptimizer provides operators with direct setpoint guidance to achieve optimal plant conditions. The rigorous model accounts for current inlet volumes/compositions, processing equipment capability (current fouling and efficiencies), producer contracts, and current economic conditions, maximizing return on plant assets.
Gas Plant Optimization
The eSimOptimizer solution captures plant data (temperature, pressure, flows, and analyzer signals) and transfers the plant data over the internet to eSimulation’s data center. The data is first reconciled in a rigorous optimization model – built to match plant operations – to calibrate the model to current plant conditions. A second run optimizes the plant by suggesting setpoint targets to the operator based on the calibrated plant model, current plant data, and current plant economics.

- Maximize gas plant profitability by determining optimal product recovery targets and energy consumption
- Process monitoring and reporting
- Process engineering support
- Economic optimization
The setpoint guidance is updated on a secure web page for operator entry. The plant settles and the operator receives a new set of targets. In this way, the operator is guided to take small moves to a continuously moving optimum.
The solution monitors process performance, identifies process problems before they become production losses, monitors equipment performance to support client safety efforts, and provides direct operator guidance to optimize the gas processing facility. Use eSimOptimizer to:
Set optimal product recovery targets
Allocate the primary feeds to each cryo train
Optimally loading multi-train facilities, coordinating cryo / fractionation facilities, and capturing facility-wide profit opportunities.
Implement the value capture process (sustaining benefits)
eSimulation provides a report every two weeks describing how the optimization system is performing, provides details of the optimization moves, and identifies any issues.
Manage tradeoffs that change with market conditions
eSimOptimizer enables processors to address changes and capture value based on market conditions. The model is equally suited for ethane recovery, ethane rejection, or propane rejection operation.
"eSimOptimizer continually collects and averages relevant process data. Every 3 hours, the data is used to update equipment performance tuning factors and optimize plant operating targets based on the latest product and residue pricing.”
Scott Heiner and Dawayne Palmer
Plant Operations
Western Gas Resources, Inc.
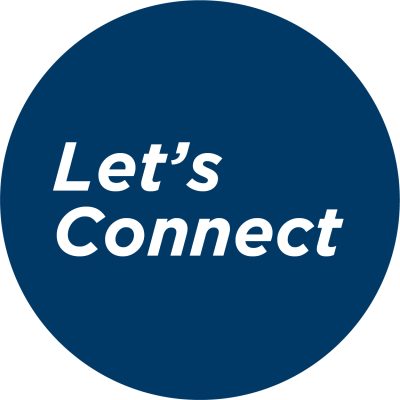
"*" indicates required fields